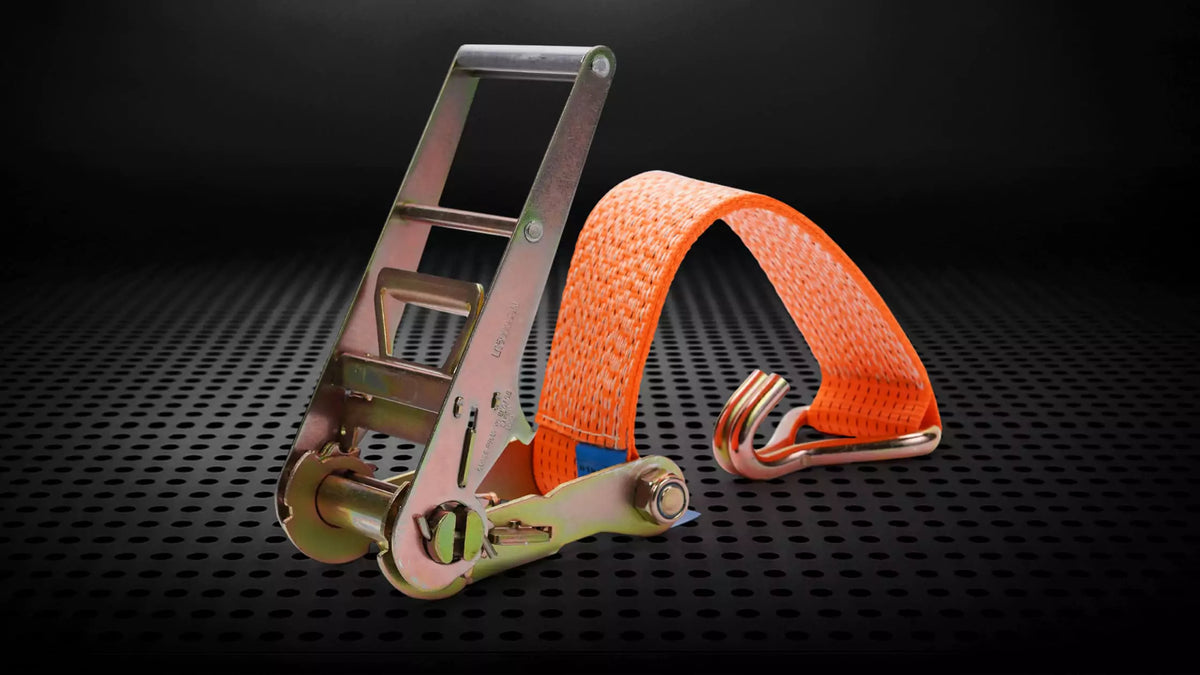
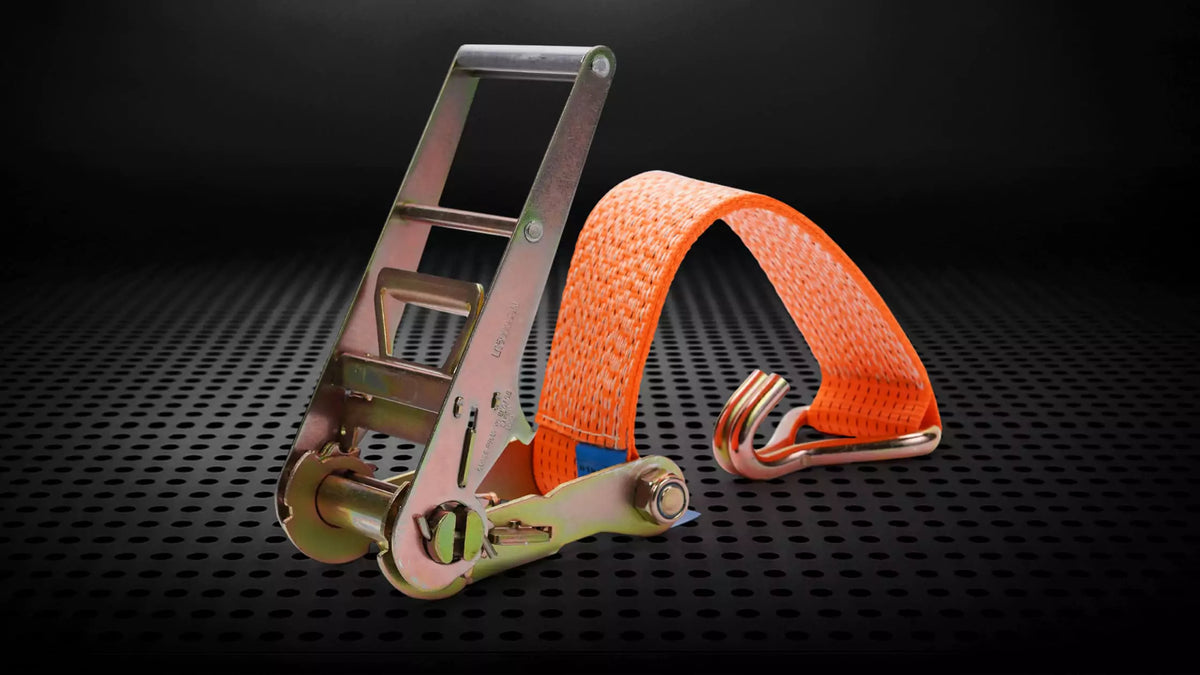
Heavy duty ratchet straps can secure massive loads up to 5,400 pounds or more. These vital cargo securement tools range from 1-inch straps for lighter loads to 4-inch heavy-duty versions. Picking the right strap is a significant factor in safety and legal compliance.
The Federal Motor Carrier Safety Administration (FMCSA) sets clear rules about cargo securement. Your cargo's length and weight determine how many tie-downs you need. A single tie-down works for loads under 5 feet and 1,100 pounds. Longer cargo requires extra straps every 10 feet.
The Working Load Limit (WLL) of your straps needs calculation by dividing the break strength by three. This ensures safe transport of your cargo.
This piece covers everything you should know about heavy duty ratchet straps. You'll learn about load ratings, DOT compliance, and proper storage techniques that make your straps last longer. These fundamentals help you secure cargo safely and quickly.
Load Ratings and DOT Compliance for Heavy Duty Straps
Load securement starts with a solid understanding of the ratings system for heavy duty ratchet straps. You need to know these key measurements to prevent accidents, equipment failure, and legal penalties whether you haul equipment commercially or secure cargo for personal transport.
Working Load Limit (WLL) vs Breaking Strength Explained
The Working Load Limit (WLL) shows the maximum safe force your heavy duty ratchet straps can handle during normal use. This rating is crucial and you should never exceed it while securing cargo. Breaking Strength indicates the point where your tie-down equipment fails completely under stress.
Heavy duty ratchet straps follow a specific safety calculation: the WLL equals 1/3 of the Breaking Strength. A ratchet strap with a 16,500-pound breaking strength will have a 5,500-pound working load limit. This safety margin helps protect against unpredictable road conditions like sudden braking, sharp turns, or rapid acceleration that add stress to your cargo securement system.
Note that a tie-down assembly's strength matches its weakest component. The entire strap's WLL defaults to 2,500 pounds if your webbing has a 3,000-pound rating but the end fitting only reaches 2,500 pounds.
DOT Compliance Requirements for Commercial Hauling
The Federal Motor Carrier Safety Administration (FMCSA) sets strict cargo securement regulations that ensure road safety. These rules state that the total working load limit of your securement system must equal at least half the weight of the cargo being transported.
Your combined WLL needs to total at least 15,000 pounds if you haul 30,000 pounds of equipment.
Here's how to calculate the total WLL correctly:
-
Count only half of each strap's WLL for tie-downs connecting from vehicle to cargo
-
Count the full WLL value for tie-downs attaching from vehicle to vehicle that pass over or through the cargo
The FMCSA requires all tie downs to stay secure without becoming loose during transit. More importantly, edge protection must shield straps from abrasion, cutting, and crushing that could damage their integrity.
These regulations can get pricey if ignored. Inspectors might issue out-of-service orders that lead to delays, missed deliveries, and extra expenses to re-secure your load.
How to Identify Legal Tags and Ratings on Straps

Every DOT-compliant heavy duty ratchet strap must have a visible, legible tag showing the manufacturer's name and Working Load Limit (WLL) in both pounds and kilograms. This tag is required by law, and in Canada, straps without proper identification must be removed from service. In the U.S., unmarked straps are still allowed, but will default to 1,000 lbs of WLL per inch of webbing width.
Some manufacturers use colored center lines on the webbing to indicate strength. According to WSTDA guidelines:
-
A single line marker indicates 5,000 lbs breaking strength per inch
-
A double line marker indicates 6,000 lbs per inch
However, these lines are not a substitute for a WLL tag, and only the sewn label is recognized for legal compliance by enforcement agencies.
Chain components in tie-down assemblies display their grade marking every seventh link (like "G70" for Grade 70 chain). The Department of Transportation requires specific working load limit ratings for each grade.
Straps become legally unusable on public roads if their WLL tag gets damaged or becomes unreadable, even with minimal wear. Inspectors will lower the strap's rating to the minimum allowed for that width without clear identification, which might make your load securement illegal.
How to Secure a Load with Ratchet Straps
Proper cargo securement prevents accidents and keeps your freight safe. Heavy duty ratchet straps remain the top choice in the industry. They provide reliable strength and can adjust to fit different types of cargo. Here's how you can use these tools the right way.
Step-by-Step Instructions: How to Use Ratchet Straps with J-Hooks
Step 1: Attach First J-Hook
- Hook one end to a secure tie-down point.
- Make sure it’s seated well and not at an angle.
Step 2: Feed the Strap Over/Through the Load
- Route the webbing over or around the cargo.
- If needed, thread through rails, bars, or loops.
Step 3: Thread the Webbing into the Ratchet
- Open the ratchet until the mandrel is accessible.
- Feed the free end of the strap through the slot in the mandrel.
- Pull through until taut, removing slack.
Step 4: Attach the Second J-Hook
- Connect the opposite hook to another anchor point.
- Keep the strap flat and untwisted.
- Pull excess webbing through the ratchet
Step 5: Ratchet to Tension
- Use the ratchet handle to crank the strap tight.
- The strap should feel firm — no wobble — but not overly tight.
Step 6: Lock the Ratchet
- Fold the handle closed until it clicks into the locked position.
- Have a final safety check before moving on
Step 7: Secure Extra Strap
- Use Velcro wraps, tie-offs, or strap keepers to secure loose ends.
- Never let extra webbing flap during transit — it can get caught or unravel.






Best Practices for Load Distribution and Tensioning
Good load distribution and tensioning keep cargo transport safe and compliant:
-
Use multiple straps to spread the tension instead of overtightening just one or two. Apply tension slowly and evenly. Pull at 45-degree angles from anchor points to get the best results.
-
The FMCSA has rules about tie-down numbers based on cargo size and weight. Loads under 5 feet and 1,100 pounds need one tie-down. Bigger or heavier loads need more straps.
-
Don't over tighten your straps. This can harm both the cargo and straps. A good tension lets you slip one finger between the strap and cargo.
-
Center your cargo on the trailer before adding straps. Balance the load to prevent movement during transit.
-
Check your load often, especially after the first 50 miles. Road vibration can loosen straps.
-
Use edge protectors where straps touch sharp edges. This stops cuts and wear that could weaken the straps.
These techniques and proper use of heavy duty ratchet straps with different securement systems will help you transport cargo safely and meet regulations.
Choosing the Right Hook and Strap Type
The right hook type and strap setup can make a huge difference in keeping your cargo secure. Each load needs specific hardware to stay safe and avoid damage while moving.

J-Hook vs Flat Hook Ratchet Straps: Pros and Cons
J-Hooks (also called wire hooks) are great for connecting to D-rings, O-rings, and trailer sides. These hooks work really well with floor plates or anchor points bolted to your flatbed.
Their compact design lets them fit into tight spaces and narrow attachment points.
Flat Hooks are stronger thanks to their wide contact area that spreads out the tie-down force. They come with a J-curve and built-in webbing defender to grip side rails firmly once tightened. So they rarely slide, even with heavy loads.
These hooks are perfect for trailer side rails but can be tough to use without railings or in cramped spaces.
When to Use Heavy Duty Tie Down Straps with Chain Ends
Chain extensions mix Grade 70 transport chain strength with polyester webbing flexibility to create a perfect solution for certain cargo. Chain ends are crucial when you need to:
-
Secure heavy equipment, especially machinery on tires or tracks
-
Attach to odd-shaped loads where regular hooks won't reach
-
Haul crushed vehicles or metal parts with few attachment spots
-
Work with loads that need cross-pattern securement to stay put
Most professional haulers like chain ends for moving equipment because they stretch less than standard webbing. While all straps stretch about 2-3% on the road, chain parts stay rigid during long hauls where even tiny movements could be dangerous.
Endless Loop vs Full Assembly Straps for Different Loads
Full assembly straps have two parts: one with an end fitting and ratchet, another with an end fitting and fixture-less end. This setup works great for most jobs where you need to secure cargo to fixed anchor points.
Endless loop straps work without hooks or end fittings. They wrap around cargo and feed back through the ratchet to make a complete loop. These special straps are perfect for:
-
Bundling cargo pallets together
-
Keeping stacked boxes from tipping
-
Securing items without good attachment points
-
Saving space by organizing loads better
These endless loop straps give you an economical option instead of plastic banding, and they're completely reusable and easier to adjust.
Inspection, Maintenance, and Storing Ratchet Straps Without Tangling
Regular maintenance of heavy duty ratchet straps acts as preventive care and will save you time and money by extending their life. A well-laid-out strap management system needs proper inspection, cleaning, and storage.
How to Inspect for Fraying, UV Damage, and Stitch Failure
You need to identify dangerous wear before it causes catastrophic failure. Check your straps before each use by looking for:
-
Frayed edges, cuts, or tears in the webbing material
-
Discoloration or stiffness that suggests UV damage (shows up as lightened areas)
-
Loose, broken, or unraveling stitching, especially at load-bearing seams
-
Missing or illegible Working Load Limit tags (makes straps legally unusable)
-
Signs of mold or mildew growth from moisture exposure
Metal components need checking for rust, corrosion, or deformation that could compromise structural integrity. Replace damaged ratchet straps right away instead of risking equipment failure during transport.
Cleaning and Drying Techniques for Strap Longevity
Your ratchet straps need cleaning after each use to maintain their integrity. A simple hosing down with clean water works for basic cleaning. For tough grime:
-
Mix mild detergent with warm water
-
Gently scrub with a quality brush to loosen debris
-
Rinse to remove all soap residue
-
Let air dry in a well-ventilated area
Complete drying is vital since moisture can cause mold and webbing deterioration. Stay away from harsh chemicals or bleach-based cleaners as they can weaken the polyester fibers.
Storage Methods: Strap Winders, Bungee Wraps, and Wall Mounts
You can avoid tangled straps with these quick storage methods:
-
Wrap the webbing around the ratchet mechanism for individual straps. Secure the hook over the wrapped portion and pull tight. Plastic zip ties, velcro cinch straps, or bungee balls work great to keep coiled straps tidy.
-
Keep your wrapped straps in plastic storage boxes, gallon-sized freezer bags, or dedicated strap duffle bags to protect them from damage. Wall mounts or E-track fittings with O-rings keep straps available yet off the floor in your workshop.
-
Store ratchet straps in dry, cool areas away from direct sunlight. UV exposure will weaken polyester fibers over time.
Common Mistakes and Limitations in Ratchet Strap Usage

Cargo securement failures can get pricey, but most happen because of basic mistakes you can avoid if you know what you're doing. Quality ratchet straps won't help much if you don't use them correctly. Your load and safety on the road depend on proper technique.
Overtightening and Load Damage Risks
Many people think tighter straps make loads more secure, but this creates systemic problems. Too much tension damages both your cargo and the straps. Your cardboard boxes and items without rigid structure might collapse under too much pressure.
The sweet spot lies in finding the right balance. You need enough tension to keep things from moving around but not so much that you distort the cargo. A steady, gradual force works best when you tighten the straps. The strap should feel snug without bending or crushing what's underneath.
Wider straps help spread out pressure more evenly for delicate items. You should also use corner protectors where straps touch sharp edges. This prevents damage to both your cargo and straps.
Using Ratchet Straps as Tow Straps: Why It's Unsafe
Ratchet straps are not designed for towing or vehicle recovery. While both ratchet straps and heavy duty tow straps are made from low-stretch polyester webbing, ideal for stability during securement, ratchet straps lack the breaking strength, width, and design features required for towing and recovery applications.
Ratchet straps typically feature narrower webbing (2–4 inches wide) and lower load ratings, making them prone to failure under towing stress. A failed strap under load can snap suddenly, turning metal components into dangerous projectiles.
For safe recoveries, always use purpose-built heavy duty tow straps. These are engineered for high break strengths (up to 380,000 lbs MBS), wider polyester webbing, and reinforced loops to handle the extreme forces encountered during towing and equipment recovery.
Using the right strap for the job isn’t just about performance — it’s about safety.
Environmental Exposure: How Weather and Conditions Affect Ratchet Strap Performance
Ratchet straps are routinely exposed to challenging conditions, and understanding how environmental factors affect them is critical for both safety and longevity.
Moisture, for instance, can accelerate mold growth and mildew if straps are stored wet, while prolonged saltwater exposure can corrode metal components, compromising the entire assembly. Similarly, UV rays degrade untreated synthetic fibers over time, reducing their working load limit (WLL) and increasing the risk of failure.
To combat these risks, many professionals now look for advanced straps that are engineered for resilience in harsh environments.
For example, premium brands like Dawnerz use:
-
Water-resistant polyester webbing that maintains its strength even when wet and resists moisture absorption.
-
UV-treated coatings to extend the strap’s usable lifespan when used outdoors.
-
Zinc-coated hardware that provides durable corrosion resistance against salt spray and humidity.
-
Low-temperature reliability, with materials rated for performance in environments as cold as −40°F.
Regardless of brand, always follow best practices:
-
Clean off salt, mud, or chemicals after use.
-
Allow straps and hardware to dry fully before storage.
-
Lubricate moving parts with non-petroleum-based silicone spray to keep ratchets functioning smoothly and minimize debris accumulation.
-
Store out of direct sunlight to prevent unnecessary UV degradation.
Choosing straps designed for real-world conditions, and maintaining them properly is key to staying compliant, reducing replacement cycles, and ensuring cargo stays secure in any environment.
Final Thoughts on Safe and Compliant Load Securement
Heavy duty ratchet straps are more than just cargo tools — they’re a frontline defense against load shifts, safety risks, and regulatory fines. Understanding their proper use, from selecting the correct WLL to routine inspections and smart storage, empowers operators to stay compliant and secure every mile of the journey.
At Dawnerz, we design our straps to meet the highest safety standards in the industry. Whether you're outfitting a flatbed, securing equipment, or managing a fleet, our heavy duty ratchet straps are built to perform under pressure.
Explore our full range of ratchet straps to make cargo securement faster, safer, and more reliable — every time.
FAQs
Q1. How do I properly secure cargo using heavy duty ratchet straps?
First, thread the strap through the ratchet mechanism and attach hooks to appropriate anchor points. Remove slack by pulling the loose end, then pump the ratchet handle to tighten. Ensure even tension across multiple straps and avoid overtightening. Always follow weight and length guidelines for the number of straps needed.
Q2. What are the key safety rules for using ratchet straps?
Follow the Working Load Limit (WLL) guidelines, which is typically 1/3 of the breaking strength. For commercial hauling, ensure the aggregate WLL equals at least half the cargo weight. Use the correct number of tie-downs based on cargo length and weight. Always inspect straps for damage before use and protect them from sharp edges.
Q3. What are some common mistakes to avoid when using ratchet straps?
Avoid over tightening straps, which can damage both cargo and straps. Never use ratchet straps as tow straps, as they lack the necessary elasticity. Don't leave strap ends dangling or secure loads at too shallow an angle. Lastly, ensure your load is balanced and avoid using damaged or UV-weakened straps.
Q4. How should I maintain and store my ratchet straps?
Regularly inspect straps for fraying, UV damage, and stitch failure. Clean them with mild soap and water, allowing them to air dry completely. Store in a cool, dry place away from direct sunlight. Use strap winders, bungee wraps, or wall mounts to prevent tangling. Replace straps with illegible or missing WLL tags.
Q5. What factors should I consider when choosing ratchet straps for different loads?
Consider the cargo weight and shape when selecting strap width and hook type. Use J-hooks for D-rings and O-rings, and flat hooks for trailer side rails. Chain-end straps are ideal for heavy equipment or odd-shaped loads. For bundling or securing items without good attachment points, consider endless loop straps. Always ensure the strap's WLL is appropriate for your cargo weight.
Further Reading & Resources
Looking to go deeper into safe cargo securement?
🔗 Synthetic Tie-Down Safety Bulletin