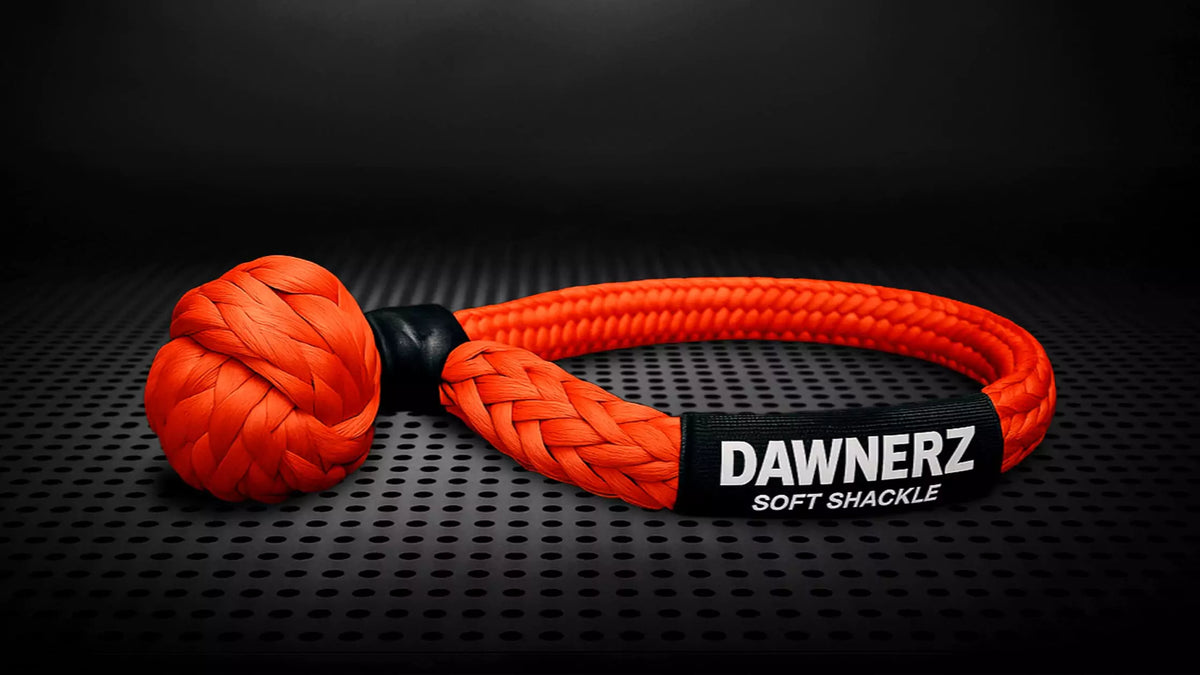
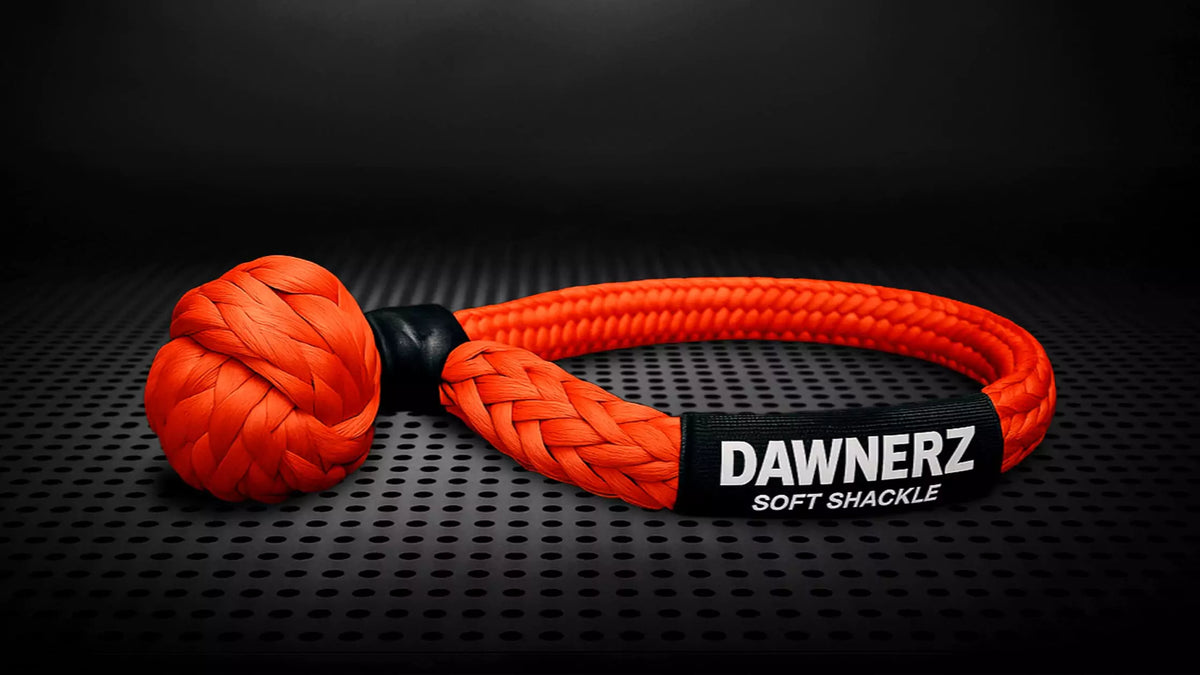
Having a reliable towing strap is essential, but incorrect connection methods can compromise the entire operation's effectiveness and safety profile.
Proper selection and connection techniques are fundamental to successful towing operations. Until recently, steel shackles dominated the market due to their proven strength characteristics and operational familiarity. However, the industry has increasingly recognized the significant safety and operational advantages offered by synthetic alternatives.
Understanding the Shift from Steel to Synthetic Shackles
The Steel Shackle Challenge
Traditional steel shackles have served the industry well, offering excellent strength ratings and wide availability. Modern steel shackles benefit from protective coatings that largely eliminate corrosion concerns in standard operating environments.
However, the primary limitation remains the failure mode. When steel shackles reach their breaking point under load, they create high-velocity projectiles that pose serious safety risks to personnel and equipment. This failure characteristic has driven many operations to reassess their connection protocols.
Synthetic Shackles: Industrial-Grade Performance
Contrary to common misconceptions, soft shackles are not limited to light-duty applications. They are successfully deployed across heavy industrial operations, including 300-tonne mining trucks and comparable heavy machinery operations. Modern synthetic fibres deliver exceptional strength-to-weight ratios whilst maintaining operational flexibility.

Key operational advantages include:
Enhanced Safety Profile: Controlled failure mode eliminates projectile hazards, significantly reducing workplace incident risk
Equipment Protection: Soft material composition prevents damage to towing points and adjacent surfaces
Operational Efficiency: Lightweight design reduces handling time and operator fatigue during deployment
Environmental Resilience: Superior performance in harsh conditions including marine environments and extreme temperatures
Storage Optimization: Compact storage requirements reduce space allocation in service vehicles
Load Rating Considerations and Compliance
Understanding Working Load Limits (WLL) and Minimum Breaking Strength (MBS) specifications is crucial for procurement decisions. Connection hardware must exceed the towing strap's breaking strength to prevent premature failure at connection points.
Industry standard safety factors typically range from 3:1 to 5:1, depending on application requirements and regulatory compliance needs. This ensures adequate safety margins whilst maintaining operational effectiveness.
Critical specification requirements:
Shackle MBS must exceed towing strap MBS
WLL ratings should align with operational load requirements
Certification standards must meet relevant industry regulations
Traceability documentation for audit compliance
Application-Specific Selection Criteria
Steel Shackles: Continued Relevance
High-frequency commercial operations requiring maximum durability
Applications demanding rigid connection characteristics
Operations where cost constraints are primary consideration
Environments where synthetic materials face chemical compatibility issues
Synthetic Shackles: Strategic Advantages
Safety-critical operations prioritizing incident prevention
Multi-vehicle fleets requiring standardized safety protocols
Operations in corrosive environments
Applications where equipment damage costs are significant
Mobile response units requiring lightweight equipment packages
Implementation and Maintenance Protocols
Proper implementation requires establishing clear inspection protocols and replacement schedules. Steel shackles require monitoring for stress cracking and pin deformation. Synthetic shackles need assessment for fibre degradation, UV exposure damage, and abrasion wear.
Documentation of inspection schedules and replacement criteria supports compliance requirements whilst ensuring operational readiness. Training protocols should address proper deployment techniques and failure recognition for both connection types.
Strategic Procurement Considerations
The transition to synthetic shackles represents a strategic investment in operational safety and efficiency.
Whilst initial procurement costs may exceed traditional steel alternatives, the total cost of ownership calculation should include:
Reduced incident-related costs and downtime
Lower equipment damage rates
Improved operational efficiency through weight reduction
Extended service life in challenging environments
Enhanced regulatory compliance positioning
Conclusion
Modern towing operations require connection solutions that balance performance, safety, and operational efficiency. Synthetic shackles offer compelling advantages for many applications, particularly where safety considerations and equipment protection are paramount.
The decision between steel and synthetic shackles should be based on comprehensive operational requirements assessment, including load specifications, environmental conditions, safety protocols, and total cost considerations. Both technologies have appropriate applications within professional towing operations when properly specified and implemented.